Composite Hose
We fit up swage composite hoses in Tasmania.
Now fitted with STATLOCK Camlock fittings.....
|
![]()
|
Petrol Composite Hose (Comp 1000 Petrol)
Construction
A robust but light weight hose designed for ease of use as a road tanker delivery hose for petrol, diesel and low viscosity oils. Inner and outer wires are high tensile strength mild steel with a galvanised coating to reduce corrosion. The hose is lined and reinforced with polypropylene fabrics and sealed with polypropylene films.
The cover is a wear and weatherproof layer of PVC coated polyester. Standard colour is green but other colours can be arranged.
Inner Wire - Galvanised Steel
Reinforcement - Polypropylene Fabric and Films
Outer Wire - Galvanised Steel
Construction
A robust but light weight hose designed for ease of use as a road tanker delivery hose for petrol, diesel and low viscosity oils. Inner and outer wires are high tensile strength mild steel with a galvanised coating to reduce corrosion. The hose is lined and reinforced with polypropylene fabrics and sealed with polypropylene films.
The cover is a wear and weatherproof layer of PVC coated polyester. Standard colour is green but other colours can be arranged.
Inner Wire - Galvanised Steel
Reinforcement - Polypropylene Fabric and Films
Outer Wire - Galvanised Steel
Nominal Dia. | Working | Pressure | Min. Bend | Radius | Per Mtr | lb/ft | ||
mm | inches | kPa | psi | mm | inches | kg. | ||
25 | 1 | 700 | 101.5 | 50 | 2 | 1.08 | 0.7 | |
38 | 1.5 | 700 | 101.5 | 75 | 3 | 1.29 | 0.9 | |
50 | 2 | 700 | 101.5 | 80 | 3 | 1.87 | 1.3 | |
65 | 2.5 | 700 | 101.5 | 90 | 3.5 | 2.47 | 1.7 | |
80 | 3 | 700 | 101.5 | 125 | 5 | 2.96 | 2 | |
100 | 4 | 700 | 101.5 | 220 | 8.6 | 3.86 | 2.6 |
Nominal bore mm | Outside dia mm | Bend radius mm | Pressure nominal psi & bars | Weight kg/mtr | |
25 | 38 | 90 | 150 | 10 | 1.0 |
38 | 52 | 125 | 150 | 10 | 1.6 |
50 | 64 | 160 | 150 | 10 | 1.8 |
65 | 80 | 180 | 150 | 10 | 2.6 |
75 | 92 | 220 | 150 | 10 | 3.0 |
100 | 120 | 350 | 150 | 10 | 5.4 |
All pressures are based on a safety factor of 4:1 |
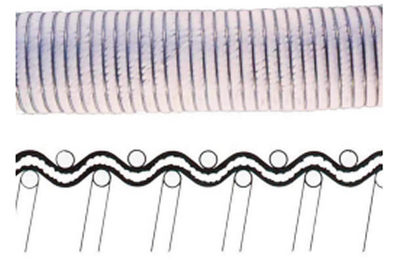
Transheat Composite Hose (Tar & Bitumen)
Description
Composite hose made from polyester and polyamide fabrics and films with an outer cover of fibreglass. Inner and outer wires are galvanised mild steel.
Classification Heat Group 6 Hose.
Colour code
White outer cover with word ‘Transheat’ stencilled.
Manufacture Transheat is suitable for temperatures to +150°C continuous and to +180°C in surges, however, pressure ratings should be reduced by 50% when temperatures exceed 100°C.
Principal applications Ideal for the transfer of most hot fluids at elevated temperatures.
Standard production length 20 mtrs
Description
Composite hose made from polyester and polyamide fabrics and films with an outer cover of fibreglass. Inner and outer wires are galvanised mild steel.
Classification Heat Group 6 Hose.
Colour code
White outer cover with word ‘Transheat’ stencilled.
Manufacture Transheat is suitable for temperatures to +150°C continuous and to +180°C in surges, however, pressure ratings should be reduced by 50% when temperatures exceed 100°C.
Principal applications Ideal for the transfer of most hot fluids at elevated temperatures.
Standard production length 20 mtrs

composite_hose_transheat.pdf | |
File Size: | 194 kb |
File Type: |
Nominal bore mm | Outside dia mm | Bend radius mm | Pressure nominal psi & bars | |
25 | 38 | 130 | 150 | 10 |
38 | 50 | 160 | 150 | 10 |
50 | 65 | 210 | 150 | 10 |
65 | 75 | 270 | 150 | 10 |
75 | 90 | 300 | 150 | 10 |
100 | 120 | 400 | 150 | 10 |
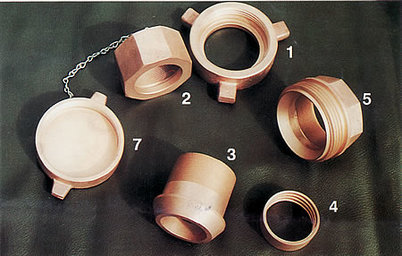
Brierley Hose & Handling are able to supply a full range of end connections to suit our composite hoses such as male and female quick release couplings, flanges, male threads and female swivel nuts.
Bitumen Fittings AS 2475
Part Number BF-1 Swivel Nut
Part Number BF-2 Gland Nut
Part Number BF-3 Lock Cone
Part Number BF-4 Hose Ferrile
Part Number BF-5 Fixed Coupling
Part Number BF-6 Dust Plug (Not shown)
Part Number BF-7 Cap
Bitumen Fittings AS 2475
Part Number BF-1 Swivel Nut
Part Number BF-2 Gland Nut
Part Number BF-3 Lock Cone
Part Number BF-4 Hose Ferrile
Part Number BF-5 Fixed Coupling
Part Number BF-6 Dust Plug (Not shown)
Part Number BF-7 Cap
Also fitted with Statloc camlocks
Care and Maintenance of Composite Hoses
Installing
Incorrect installation of a hose assembly will create stresses within the assembly and result in a premature failure. The following guidelines should be followed:
- hose assemblies must not be twisted either during installation or in use
- hoses must not be overflexed or bent into a smaller diameter than the specified minimum bend radius
- hose assemblies should be installed so that flexing always occurs in the same plane
- it is recommended that flanged assemblies have a floating flange on one end for easier installation and to reduce the possibility of twist handling
Hoses should be stored in a straight line on solid supports or racks.
Large bore hoses should be carried on a dollie or moved by crane. Hoses must not be supported by a single rope or wire. A wide belt sling should be used, supporting the hose at least every 3 metres.
Avoid curvatures that are less than the minimum bend radius of hose.
Do not allow sharp bends adjacent to the end connection fitting - this area is the weakest spot in any type of hose. Support the hose.
Hoses should not be dragged along the ground or over guard rails. Do not allow the hose to chafe (rub) against hard surfaces and/or sharp edges.
If unavoidable, consider having the hoses rope lagged.
Cleaning
Before storage, hoses should be drained and flushed with clean water to remove dangerous vapours, the exception being hoses which have been used for conveyants such as sulphuric acid when dilution with water could leave a very corrosive residue. In such instances, drain dry.
Hoses must be electrically earthed during cleaning operations.
Hoses may be cleaned using low pressure air, however hoses must be open-ended to avoid excessive pressure build up.
Steam is not recommended for cleaning as the excessive temperature involved (over 100°C) will damage the hose fabrics. inspection Inspect hose for visual damage at least every six months, more often if experience demands it.
Look for:
1. Weakening of the hose adjacent to the end fitting
2. Cuts and abrasions on the fabric cover
3. Abrasion of the outer wire
4. Displacement of the outer wire - identified by differing widths between each round of wire over the length
5. Dents, kinks or twisted sections testing
Composite hose assemblies should be hydrostatically tested at least once every twelve (12) months and electrical continuity tested, where applicable, at least once every six(6) months.
Care and Maintenance of Composite Hoses
Installing
Incorrect installation of a hose assembly will create stresses within the assembly and result in a premature failure. The following guidelines should be followed:
- hose assemblies must not be twisted either during installation or in use
- hoses must not be overflexed or bent into a smaller diameter than the specified minimum bend radius
- hose assemblies should be installed so that flexing always occurs in the same plane
- it is recommended that flanged assemblies have a floating flange on one end for easier installation and to reduce the possibility of twist handling
Hoses should be stored in a straight line on solid supports or racks.
Large bore hoses should be carried on a dollie or moved by crane. Hoses must not be supported by a single rope or wire. A wide belt sling should be used, supporting the hose at least every 3 metres.
Avoid curvatures that are less than the minimum bend radius of hose.
Do not allow sharp bends adjacent to the end connection fitting - this area is the weakest spot in any type of hose. Support the hose.
Hoses should not be dragged along the ground or over guard rails. Do not allow the hose to chafe (rub) against hard surfaces and/or sharp edges.
If unavoidable, consider having the hoses rope lagged.
Cleaning
Before storage, hoses should be drained and flushed with clean water to remove dangerous vapours, the exception being hoses which have been used for conveyants such as sulphuric acid when dilution with water could leave a very corrosive residue. In such instances, drain dry.
Hoses must be electrically earthed during cleaning operations.
Hoses may be cleaned using low pressure air, however hoses must be open-ended to avoid excessive pressure build up.
Steam is not recommended for cleaning as the excessive temperature involved (over 100°C) will damage the hose fabrics. inspection Inspect hose for visual damage at least every six months, more often if experience demands it.
Look for:
1. Weakening of the hose adjacent to the end fitting
2. Cuts and abrasions on the fabric cover
3. Abrasion of the outer wire
4. Displacement of the outer wire - identified by differing widths between each round of wire over the length
5. Dents, kinks or twisted sections testing
Composite hose assemblies should be hydrostatically tested at least once every twelve (12) months and electrical continuity tested, where applicable, at least once every six(6) months.